2. Fabricating high-precision, multifunctional semiconductors
Semiconductor lithography systems, which are indispensable for semiconductor manufacturing, use ultra-high-performance lenses to reduce highly complex circuit patterns drawn on a photomask made of a large glass plate, so that they can be printed onto silicon wafers.
If even a tiny bit of dust gets onto the lens or the wafer while a semiconductor that requires extremely fine processing at the nanometer level is being fabricated, it is not possible to etch the circuit accurately. It is therefore necessary to use a cleanroom where dust and dirt can be reduced to an absolute minimum. Workers in a cleanroom environment need to wear full-body garments to prevent dust or other foreign particles from getting onto the equipment.
1. Slicing a silicon wafer
A cylindrical, high-purity silicon ingot is cut into discs to make silicon wafers with orientation notches.
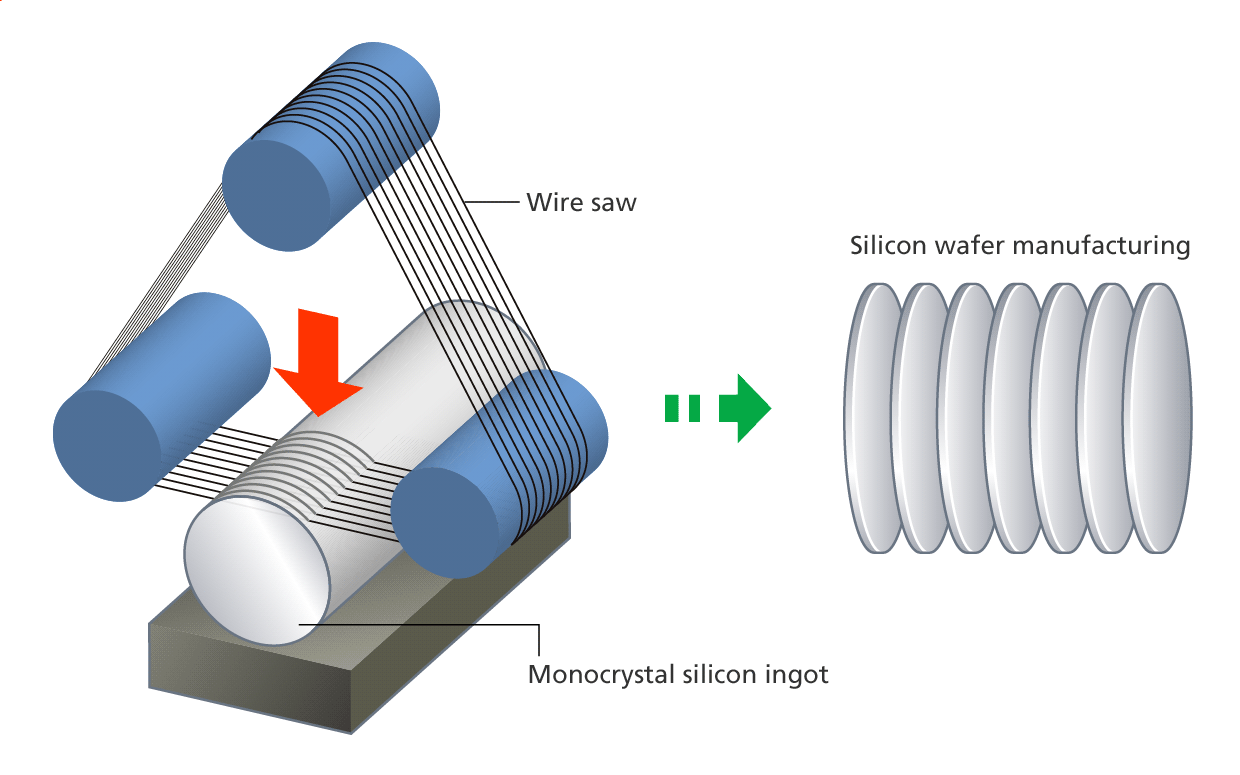
2. Forming oxide film
The silicon wafers are lined up and annealed in a furnace with the addition of oxygen and silicon gas to produce an oxide film on the surface.
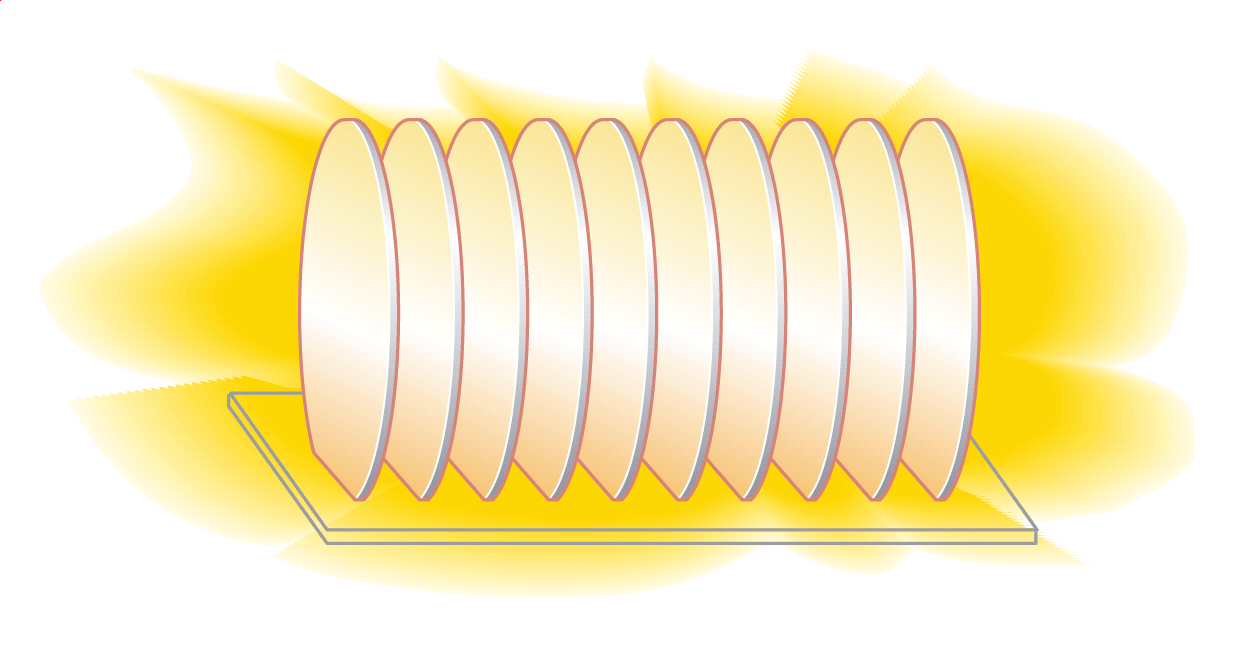
3. Applying photoresist
Next, a photosensitizing agent known as photoresist is applied to the surface. The silicon wafer is rotated at high speed during the coating process so that the photoresist is applied thinly and uniformly onto the wafer.
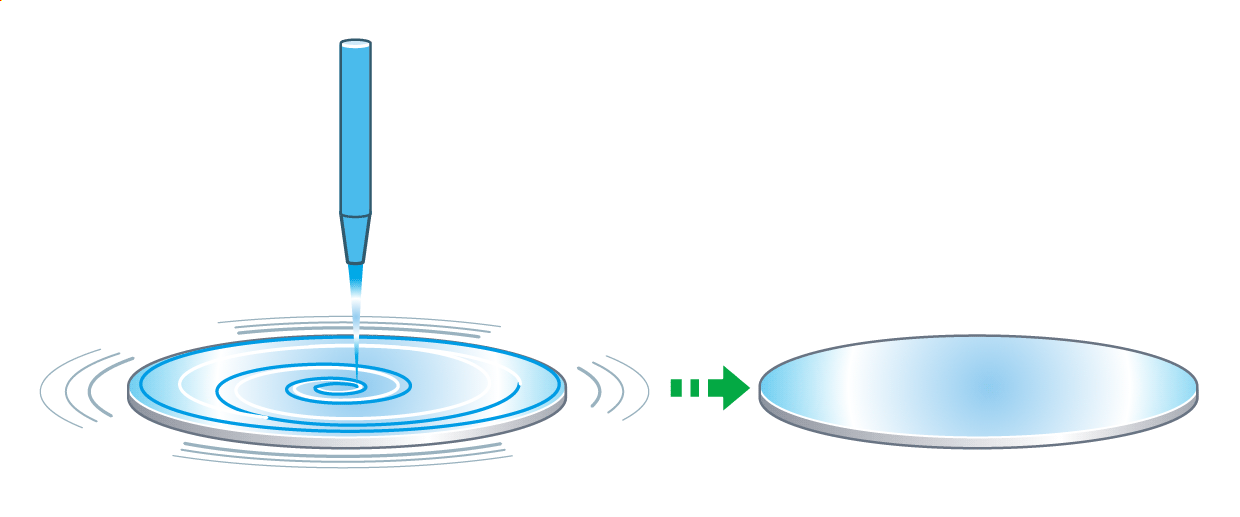
4. Exposing
A semiconductor lithography system aligns the silicon wafer and the photomask, reduces the electronic circuit pattern on the photomask to a quarter or a fifth of the size through a lens, then projects light on the circuit pattern to pattern it on the silicon wafer.
Exposure is done chip by chip. Various elements are formed on the silicon wafer by using different photomasks. Processes 3 to 7 are repeated several tens of times.
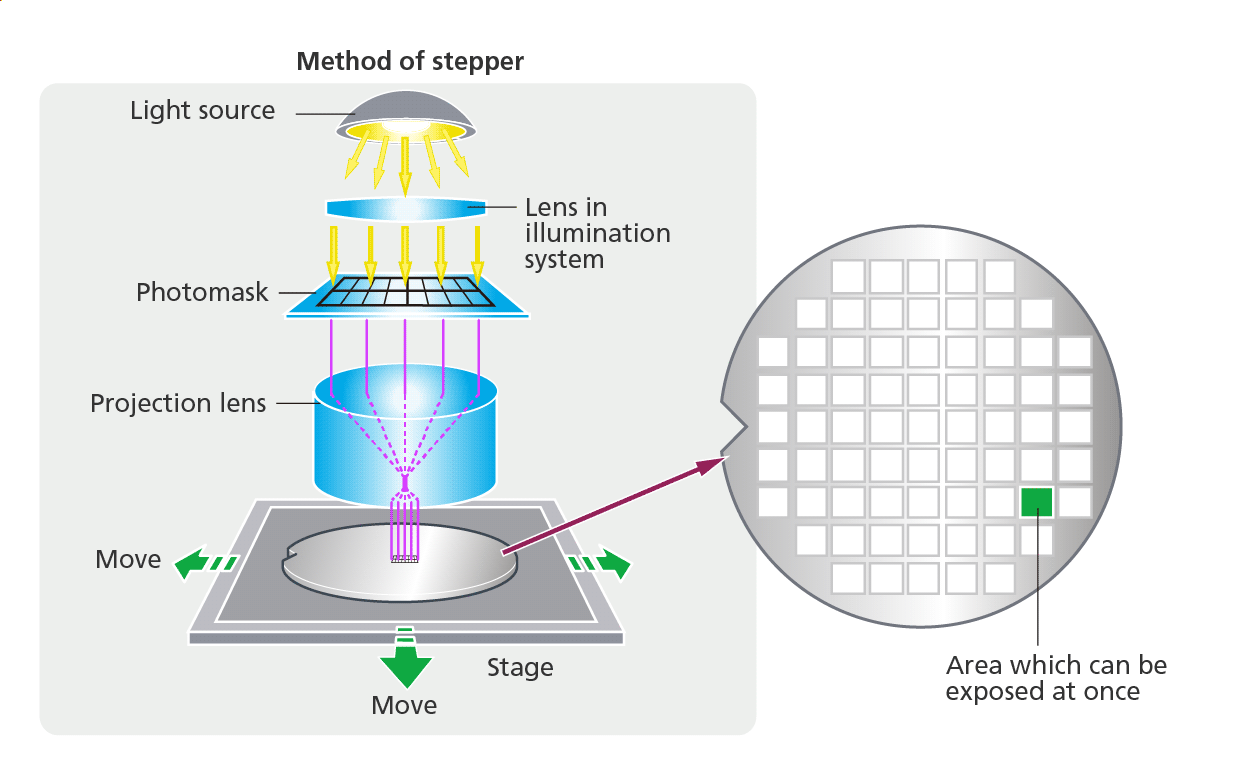
5. Developing
In the development process, the photoresist of the exposed areas is dissolved by immersing the wafer into a liquid solvent. The oxide film under the exposed areas is revealed.
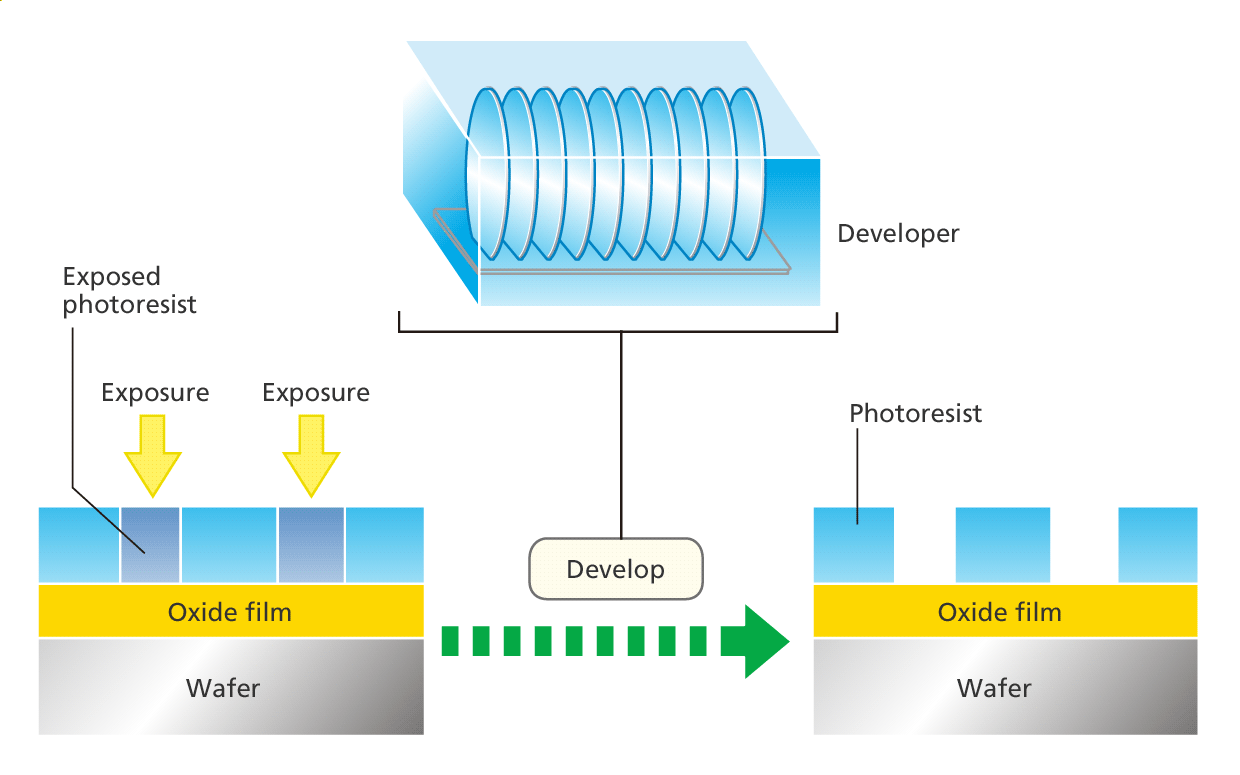
6. Etching
After the revealed oxide film has been removed, the remaining unwanted photoresist is removed to reveal the patterns.
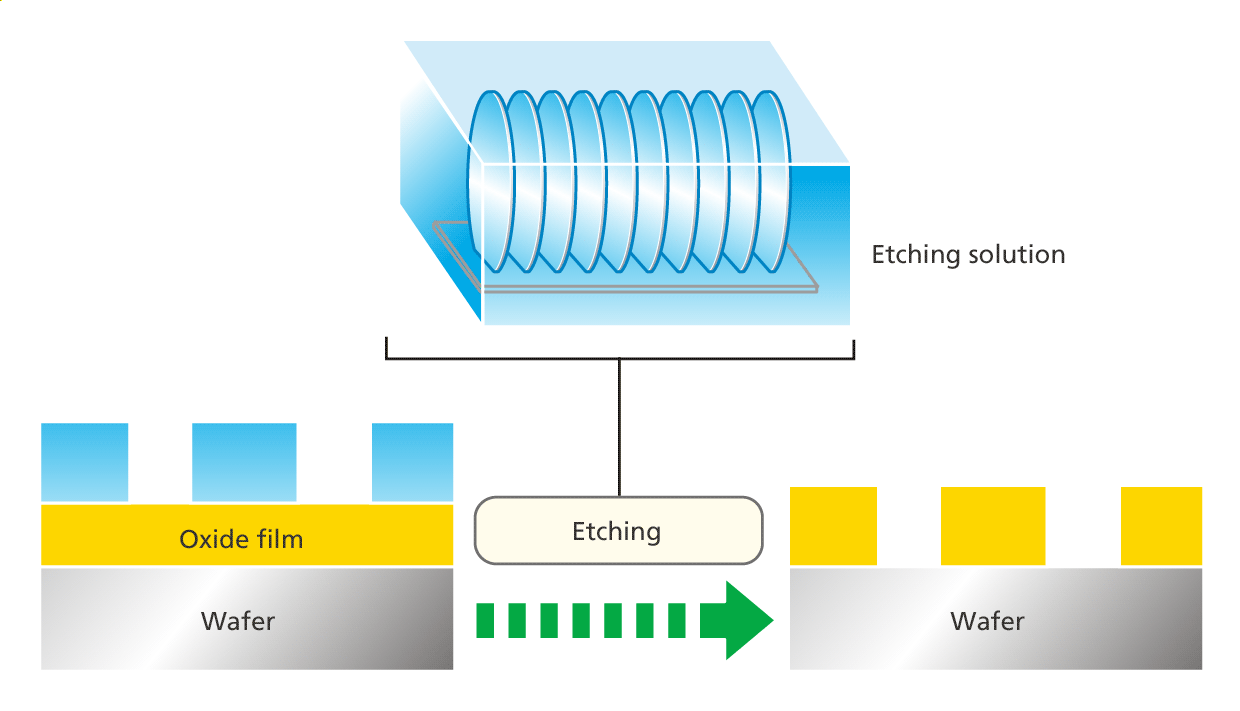
7. Doping
The transistors, diodes and other elements are formed on the silicon wafer by adding chemicals such as boron, phosphorus, and arsenic to the wafer in a furnace.
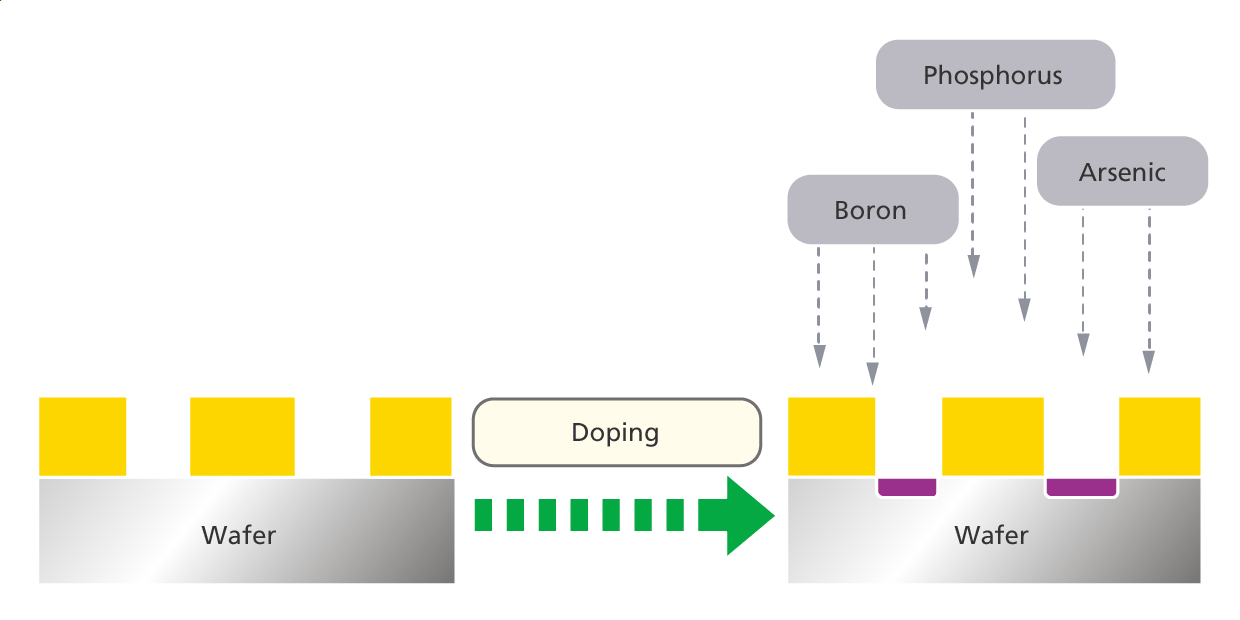
8. Wiring
To connect the elements formed on a silicon wafer, aluminum is deposited onto the surface, and aluminum on unwanted areas is removed.
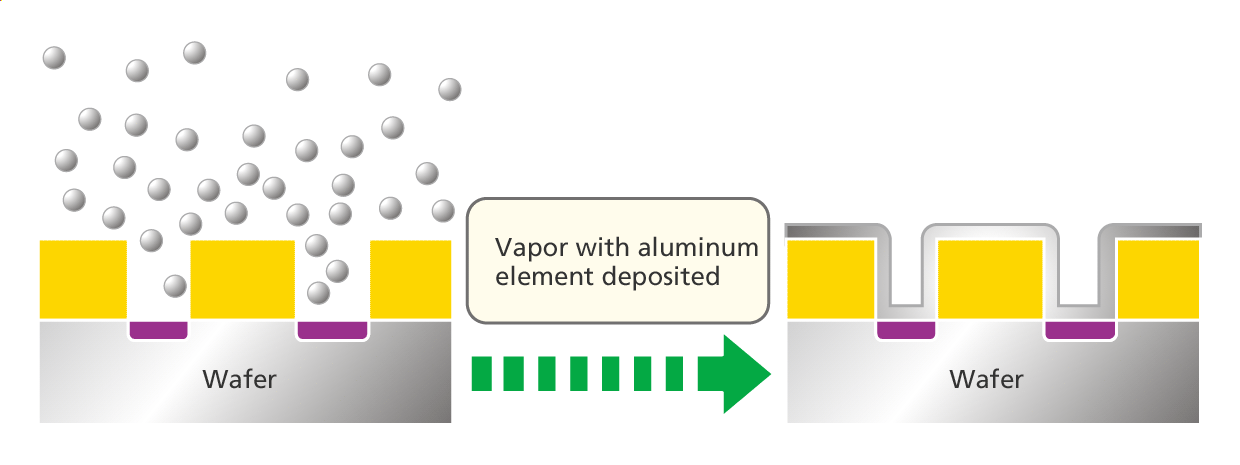
9. Dicing
The chips on the silicon wafer are cut off one by one.
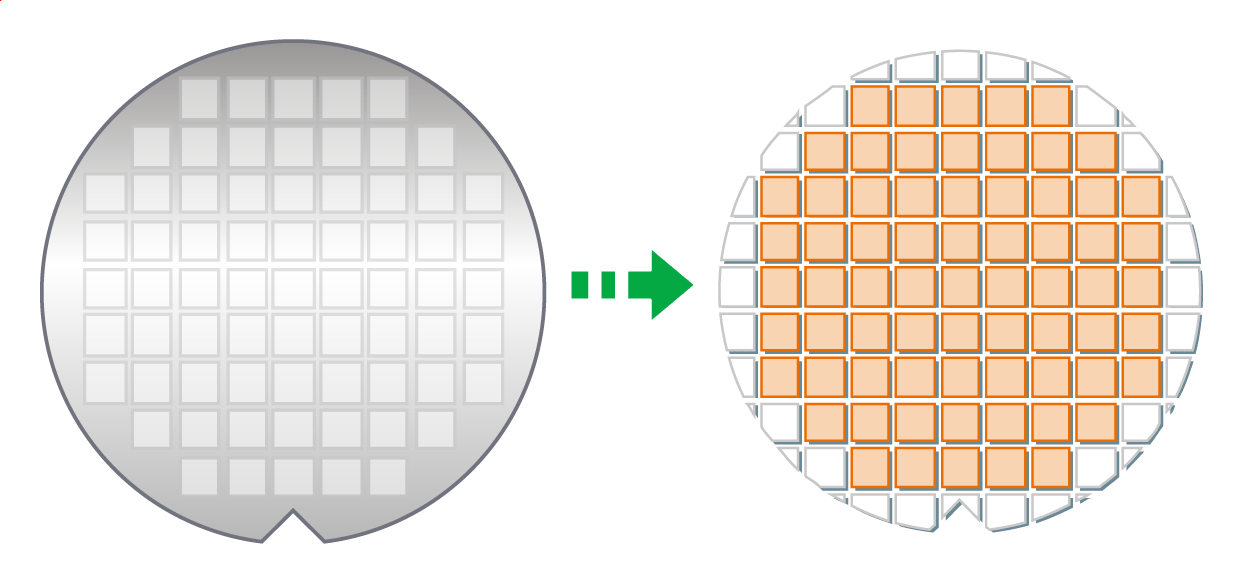
10. Bonding / Molding
The chips and leadframes (the frame for connecting the chip to the terminals) are then connected via thin gold wires.
The chips are enclosed in synthetic resin or ceramic packages to protect them from shock and scratches.
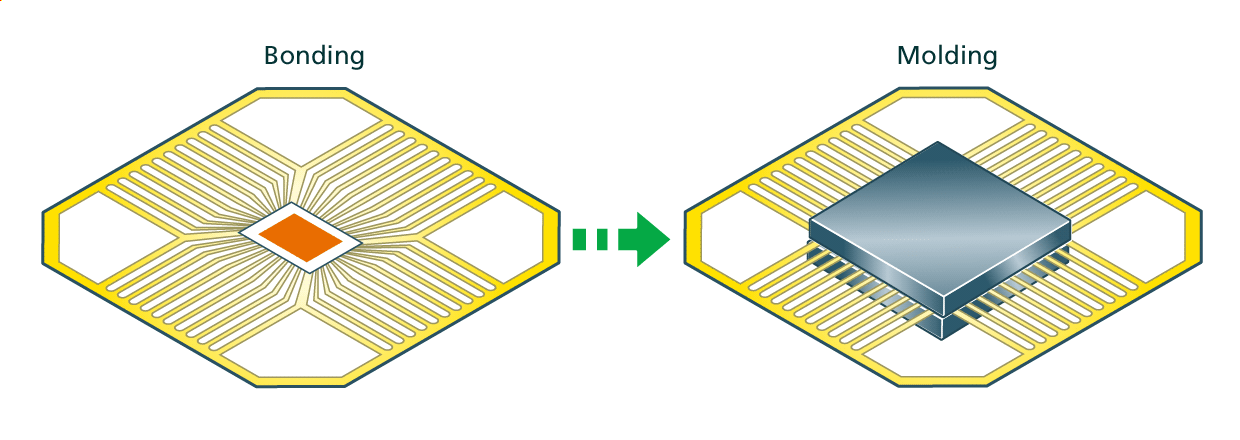
11. Semiconductor completion
The frame section is removed and leads are shaped so that the semiconductor can be mounted on a board.
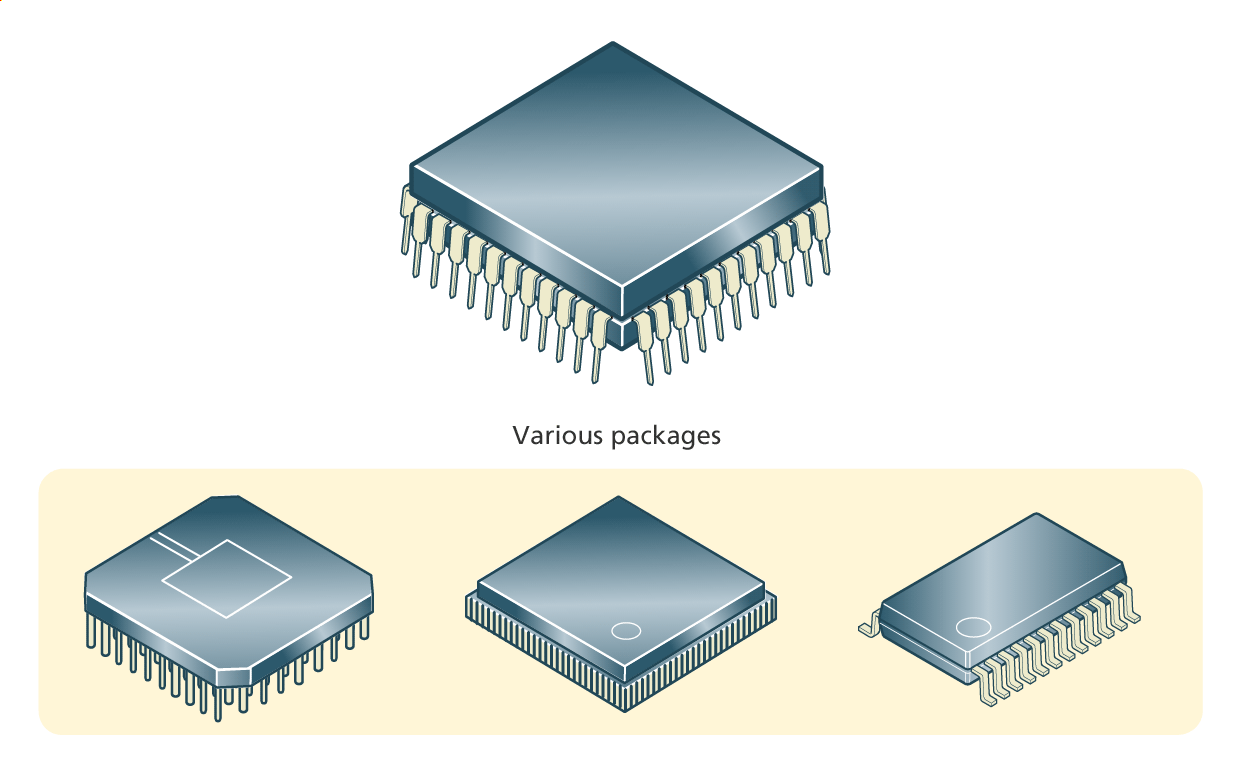
- 1. What is a semiconductor, a device that's so small, yet so essential to everyday life?
- 2. Fabricating high-precision, multifunctional semiconductors
- 3. A host of Nikon technologies enables semiconductor production
- 4. Immersion lithography technology supports leading-edge semiconductor production
- 5. The NSR-S635E immersion scanner realizes ultra-high precision and productivity
- 6. Total support for worldwide semiconductor production