Laser Ablation Processing
Technology Overview
This is a processing method that uses a laser to remove material, and can be applied to almost any solid material, including metals, glass, and ceramics. As a non-contact method, it easily processes complex shapes. Using an ultra-short pulse laser, in particular, minimizes thermal effects compared to other methods. Another advantage is that by combining this with high-precision measurement, no jigs are required for processing.
Laser ablation with a high-intensity, ultrashort-pulse laser directly breaks the molecular and atomic bonds that bind materials in the irradiated area. The laser used for processing is selected according to the material to be processed. Factors such as wavelength, pulse width, pulse energy, and pulse repetition frequency are considered.
It is necessary to design the focusing system and scanning optical system that direct the laser onto the material to be processed, and to set the scanning path.
The scanning path is determined by estimating the processing amount based on the pulse energy, repetition frequency, spot size, scanning speed, etc., ensuring the desired accuracy and shape.
This is used for processing high-precision metal components with complex shapes, and lens shapes that are difficult to achieve with conventional processing. It can also produce single units that would require assembling multiple components into a composite part with conventional machining methods.
The optical processing machines that we offer are also used for complex and fine shapes, such as riblets.
Technology Application Examples
Optical Processing Machines
The optical processing machine was developed by applying Nikon’s semiconductor lithography technology. The coordinate system is adjustable with high accuracy over a wide range. Therefore, model data can be accurately reproduced with high fidelity in processing. An ultra-short pulse laser is used as the light source, enabling non-thermal laser ablation processing on almost all materials. Furthermore, with a high-precision three-dimensional (3D) optical measuring device mounted on the machine, accurate feedback of measurement results to the laser processing enhances process quality. The machining path is automatically generated from computer-aided design (CAD) data, processing parameters, and 3D measurement results, allowing sub-micrometer processing accuracy without relying on the operator’s skill.

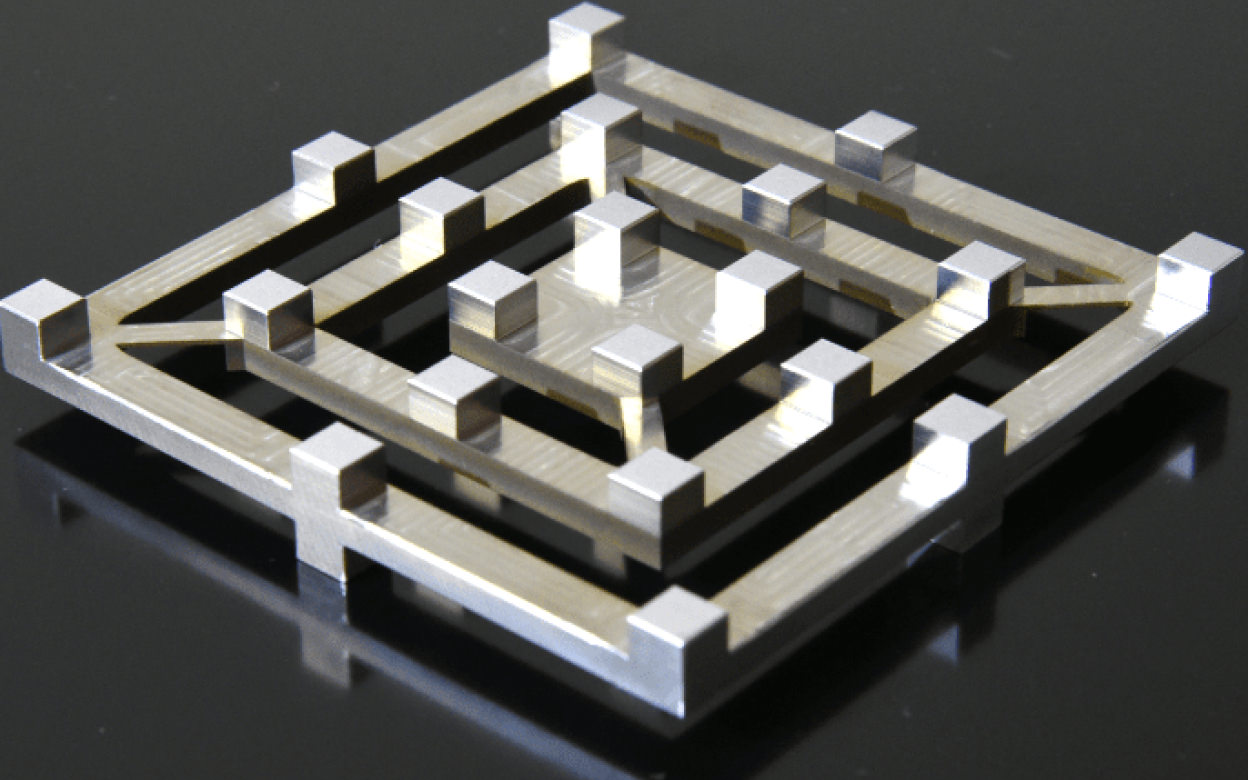
Technologies related to these examples
Related Technology
Optical Processing
By machining using light, it is possible to machine without contact, and there are few restrictions on machining, making it possible to process complex and small shapes. By selecting the appropriate light, a wide range of materials can be processed. For example, in additive processing of metals, there are methods such as the powder bed fusion (PBF), in which metal powder is spread out and then partially melted and solidified with a laser depending on the processing size and precision, and the directed energy deposition method (DED), in which metal material is melted with a laser and layered.
Nikon’s optical processing machines are used to repair parts and are required to create shapes quickly and with high precision. Riblet processing, which forms fine structures on the surface of aircraft bodies to reduce frictional resistance, requires the efficient processing of large workpieces. It is also used to create high-precision, complex components in lithography systems, etc.
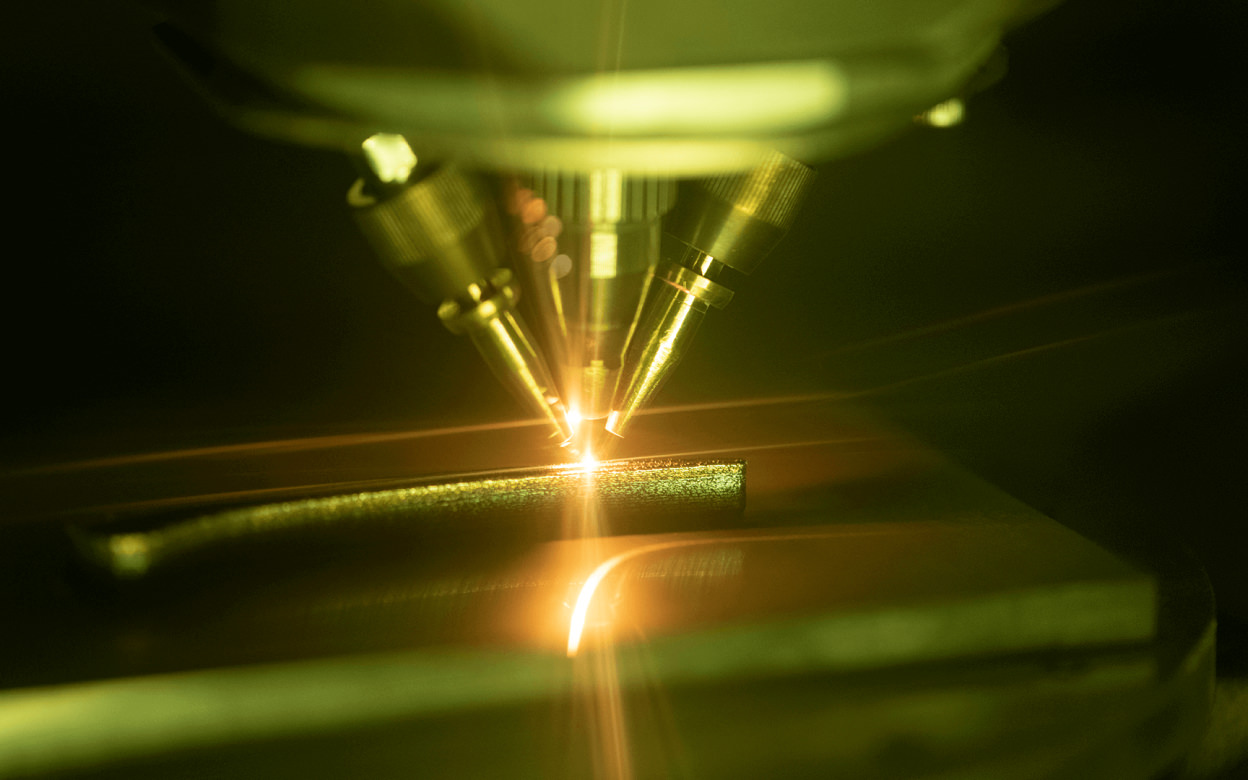
Main Related Products
You can search for articles related to Nikon’s technology, research and development by tag.