Supporting manufacturing through highly precise,
non-destructive inspection

Protecting safety with X-ray inspection systems
The XT H 450 CT inspection system performs quality inspection of
aircraft and vehicle parts, helping to ensure reliability.
We make effective use of X-ray systems in the fields of manufacturing
and R&D to contribute to a safer society.
Aircraft safety depends on reliable parts
Many people fly regularly on business or travel, but have you ever wondered about what goes into a commercial aircraft? There are said to be about three million parts in a medium- or large-sized aircraft, which is almost impossible to imagine. Yet aircraft are also described as the "safest of all vehicles," with each part needing to be completely reliable. That means careful quality inspection is an indispensable part of the manufacturing process — for every component.
Components that play a crucial role are turbine blades, which conduct the high-pressure, high-temperature gas produced by the jet engine combustor. Unless turbine blades are manufactured to the exact design specifications, not only will their energy conversion efficiency be reduced, but unexpected problems may also arise. As they are exposed to temperatures as high as about 1,000°C/1,832°F, the thickness of blades is designed to ensure an optimum balance between the strength of their entire surface and their cooling ability, with a strictly defined margin of error. Of course, there is also a risk of structural defects such as cracks and cavities shortening the life of blades. It is necessary to strictly inspect the accuracy of the blade shape, wall thickness, as well as detect structural defects. All items in the manufacturing process are subject to these inspections.
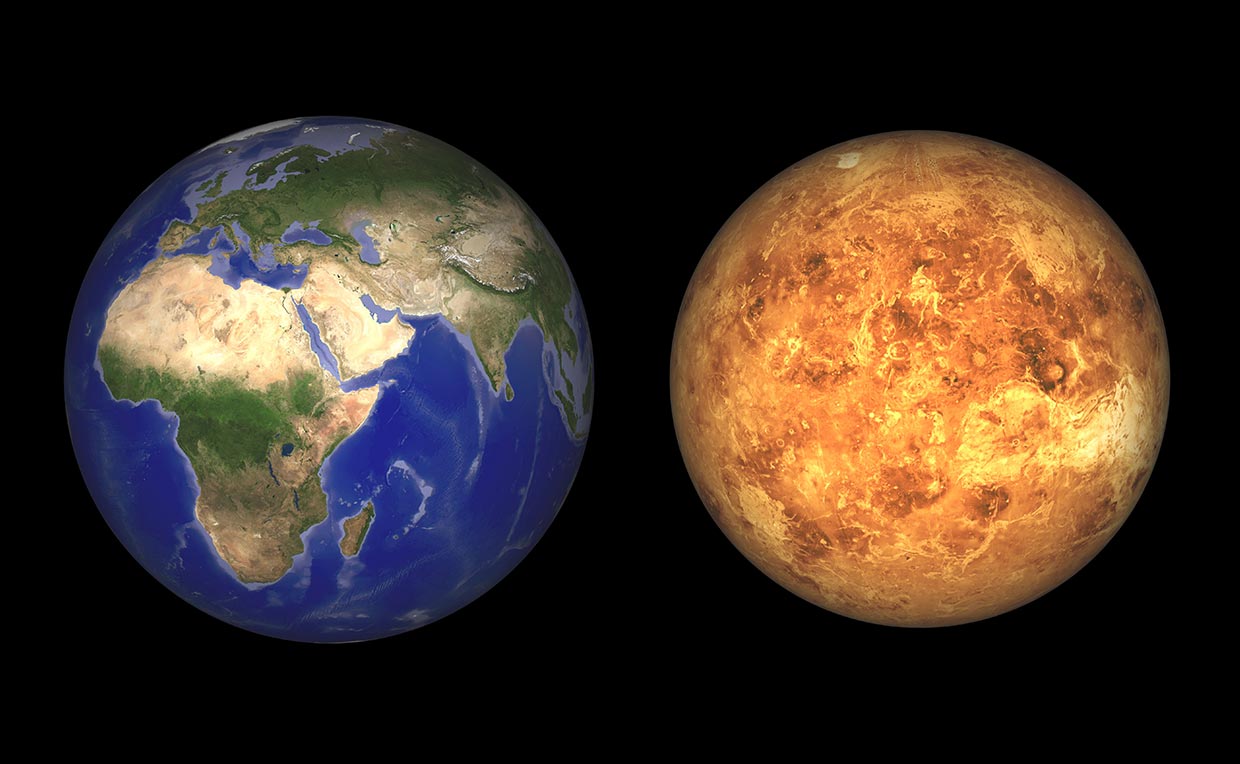
These inspections are generally performed by visualizing the internal structure using X-rays and quantifying the dimensions as a three-dimensional shape using CT based on the image data. However, turbine blades are made of high-density materials, such as single-crystal alloy, and cannot be inspected using conventional X-ray/CT inspection systems. That's where Nikon's XT H 450 CT inspection system, equipped with an X-ray source that generates high-power X-rays, comes into play.
Non-destructive, non-contact inspection to maintain manufacturing qualit
One of the key features of the XT H 450 is that it acquires images that are detailed even when enlarged since it employs a micro-focus X-ray source. Moreover, as the world's only system with a high-power, micro-focus 450 kV X-ray source, the XT H 450 is able to inspect high-density metals with high accuracy, and can be used to analyze the internal structure of turbine blades.
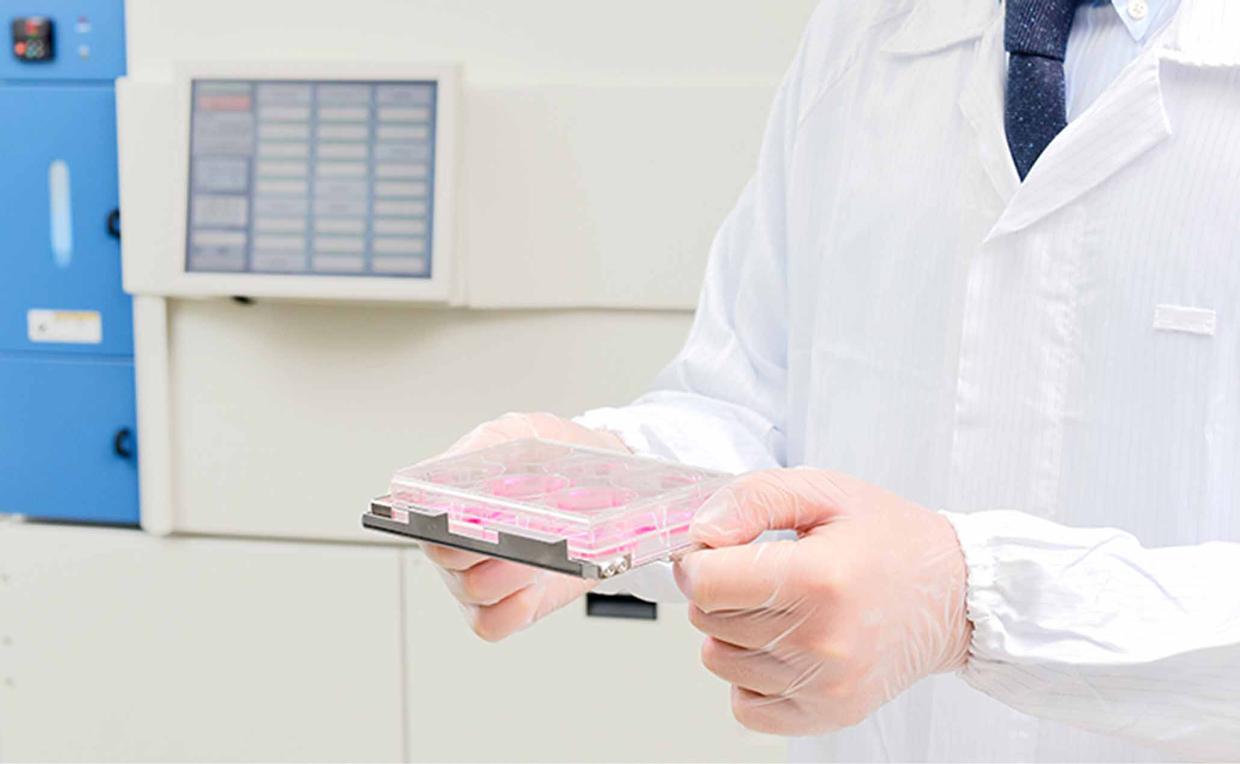
Being able to conduct non-contact, non-destructive inspection of the sample (inspecting the sample without touching or breaking it) is also a major asset. Such inspections can be incorporated into the manufacturing process, with the ability to assign each blade an automatic pass/fail, meaning that it's possible to achieve high quality and enhanced productivity at the same time. Additionally, 3D printers have begun to be utilized in the manufacturing of metal parts for aircraft. X-ray/CT inspection systems are also expected to be employed in such fields as well. Thanks to these unique benefits and the knowledge Nikon has accumulated through its work in the aerospace industry, its products are now used in a growing range of applications.
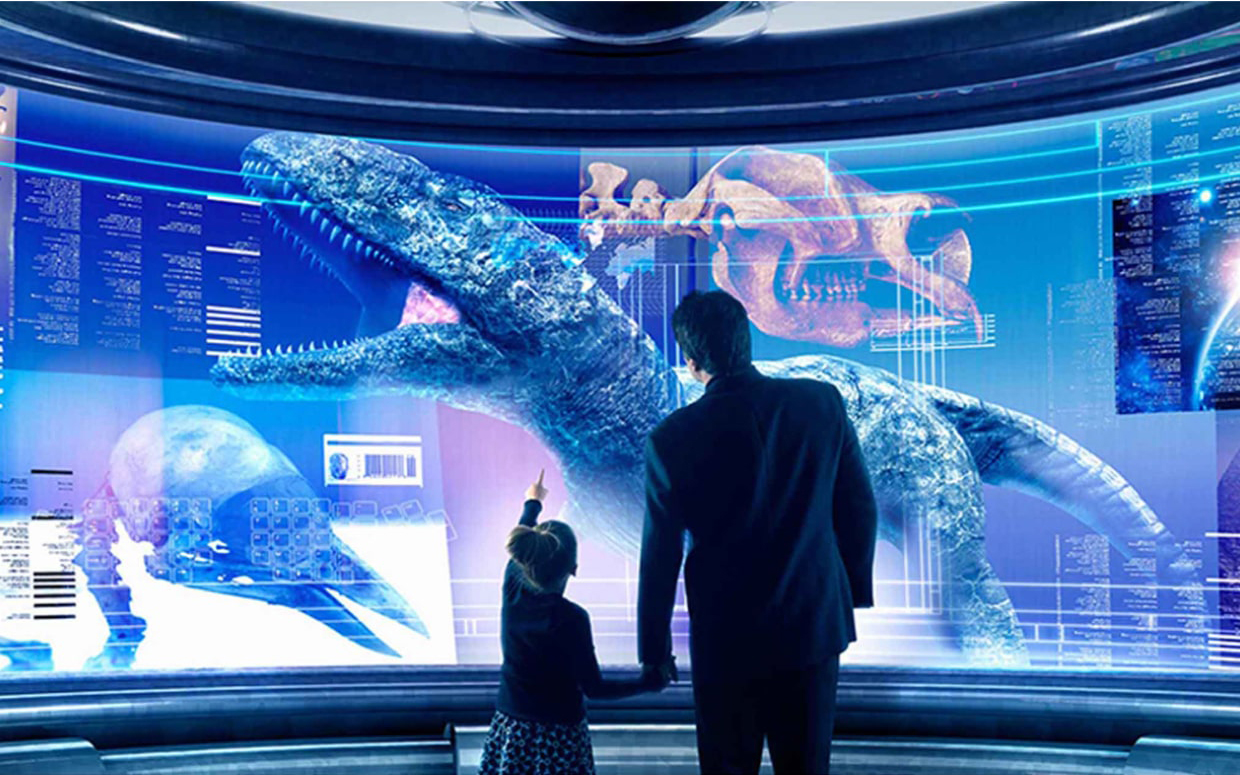
One of them is the automotive industry. Vehicles may only contain about 30,000 parts, which is one hundredth the amount used in a typical aircraft. But the production volume of vehicles is about 100 million* worldwide every year, which is more than 60,000 times that of major commercial aircraft. The total number of parts made annually exceeds that of an aircraft — and of course, each one needs to be highly reliable. At the same time, the industry has been working to improve fuel efficiency by reducing weight. For example, casted engine blocks are becoming ever thinner, and if there are defects in the internal structure, this means the risk of breakage is greater. The importance of accurate inspection is increasing, especially for realizing self-driving cars. The XT H 450 is used for inspection in such engine casting manufacturing, as well as for turbocharger R&D by providing non-destructive inspection to check the quality of casted parts and welds.
- *Reference: Order/delivery status for major commercial air transport (The Society of Japanese Aerospace Companies)
Expanding applications as an "eye" for maintaining quality
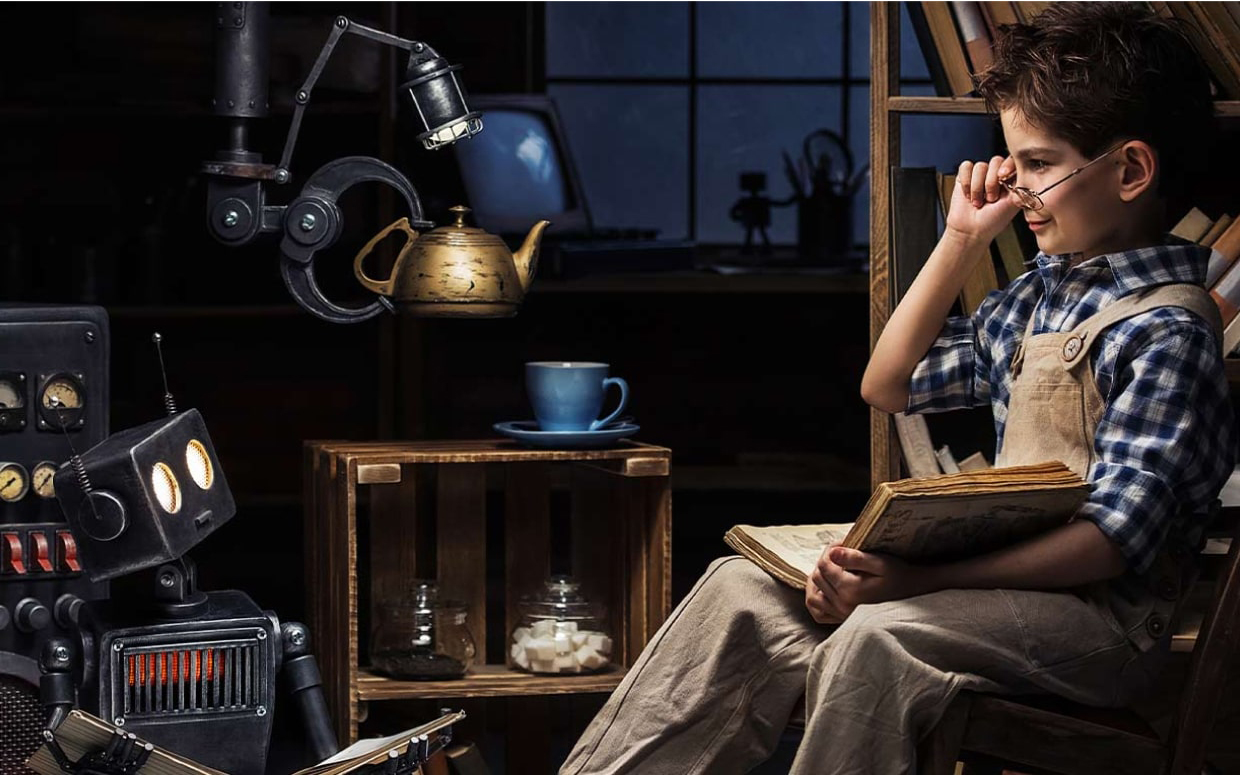
As the automotive industry worldwide is advancing from gasoline-powered to electronic vehicles (EVs), the development of and applications for vehicles using electric motors are progressing rapidly. Batteries are one of the key elements and these types of batteries are made of high-density metal and cannot be disassembled after they are manufactured. Electronic motors, another vital component of EVs, are also made using high-density metal. The XT H 450 can also be used for quality checks on these next-generation vehicles.
Nikon's XT H 450 enables efficient, non-destructive inspection with high accuracy. We continue to maintain the strictest quality standards in various manufacturing fields to contribute to the safety of lives and society.
Looking into the future of various fields with X-ray/CT inspection technology
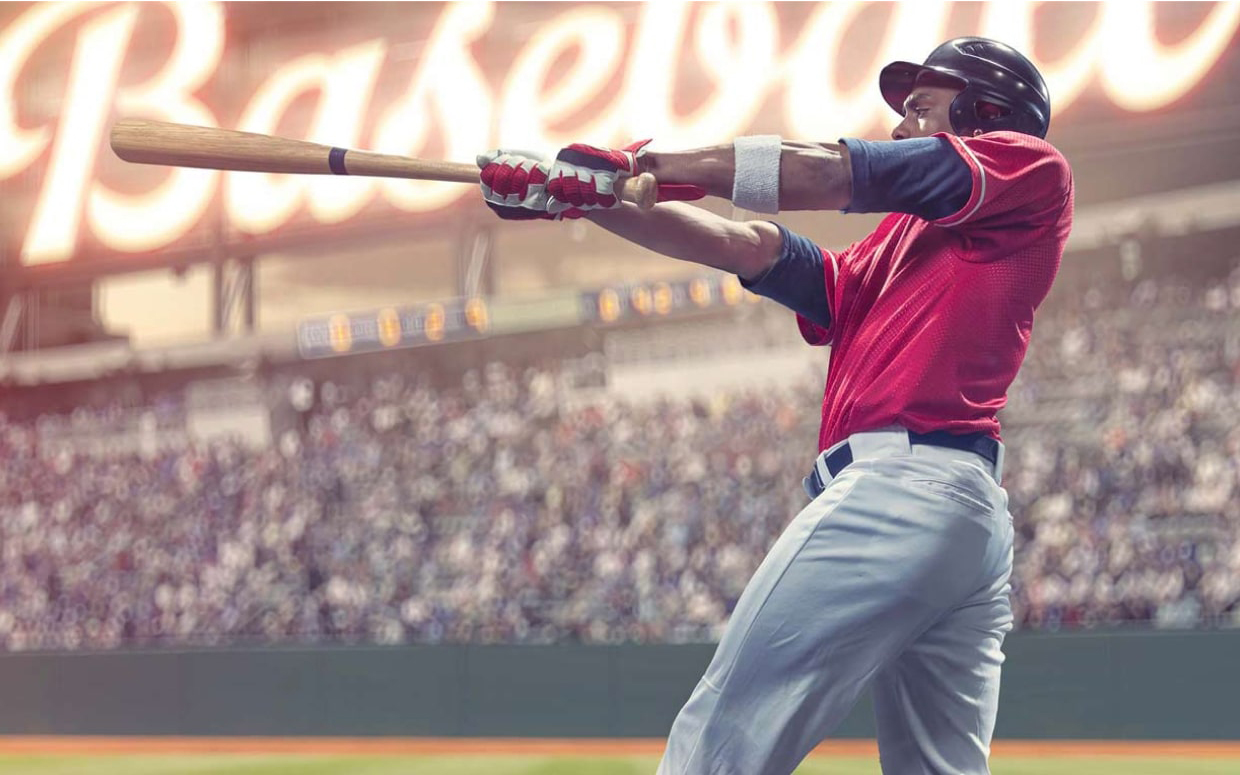
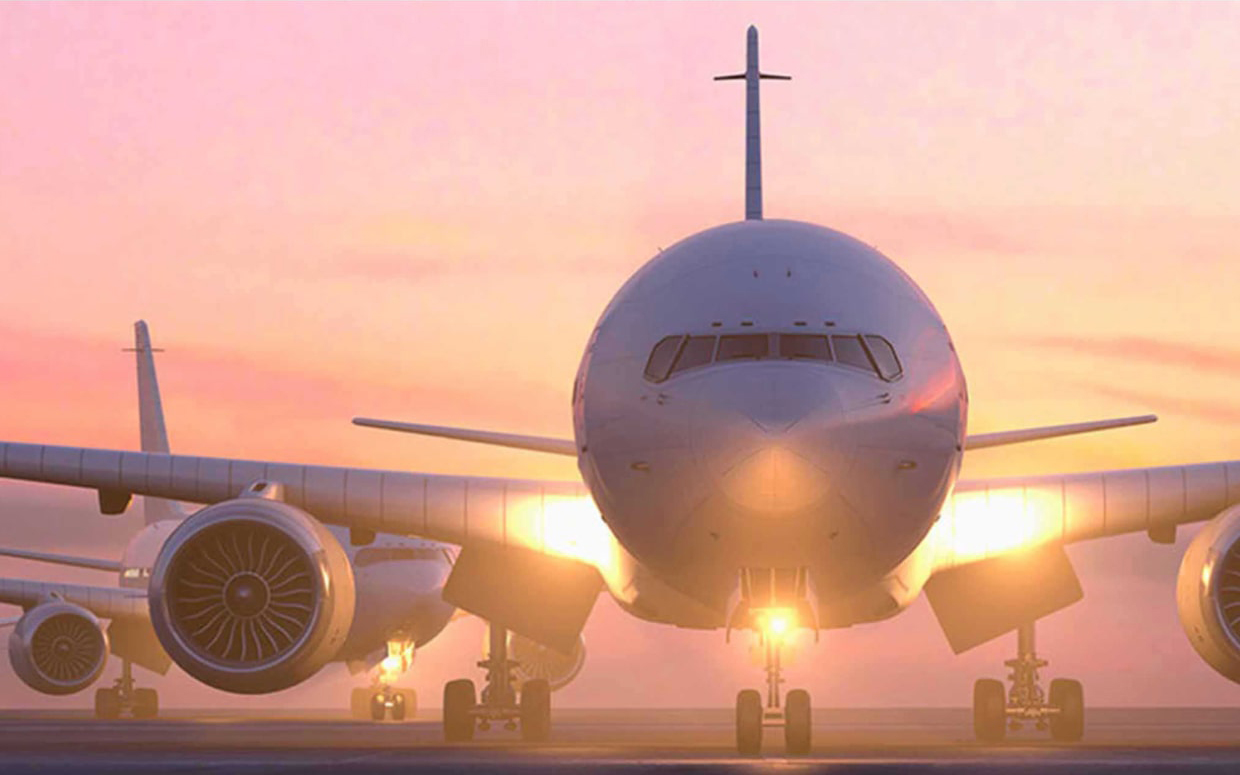
David Bate
Industrial Metrology Business Unit
(Nikon X-Tek Systems Ltd.*)
"The major part of developing X-ray/CT inspection systems is probably the problem solving. There's usually no obvious right answer, so we continue to experiment until we find something. We often talk about "peeling the onion." It's a case of taking the problem and breaking it down into smaller chunks so you can achieve small successes one after another.
We started looking at various industries, moving across to automotive. We arranged tie-ups with the Formula 1 companies quite early, and some major Formula 1 companies are using our systems during development of their cars. They're at the cutting edge, and now that we've built up experience of working in such a highly regulated, safety-conscious industry, I believe it will become the foundation for new product development in the future.
There's a wide range of industries that can benefit from X-ray/CT inspection technology, outside of the manufacturing sector. For example, archeology, history and art. Geology is another area that could grow.
It's much more efficient if you can CT a rock core and virtually deconstruct it. In soil science, you can also use CT to see how plant roots grow over time.
It's important for us to keep in touch with other industries that might take us to new leads and challenges in the future."
- *Nikon X-Tek Systems Ltd.: Develops and manufactures X-ray CT and other three-dimensional metrology products.
- *Job title and responsibilities at time of interview.
Originally published: January 7, 2019.